Process Improvement
Everything is a process and every process can be optimized
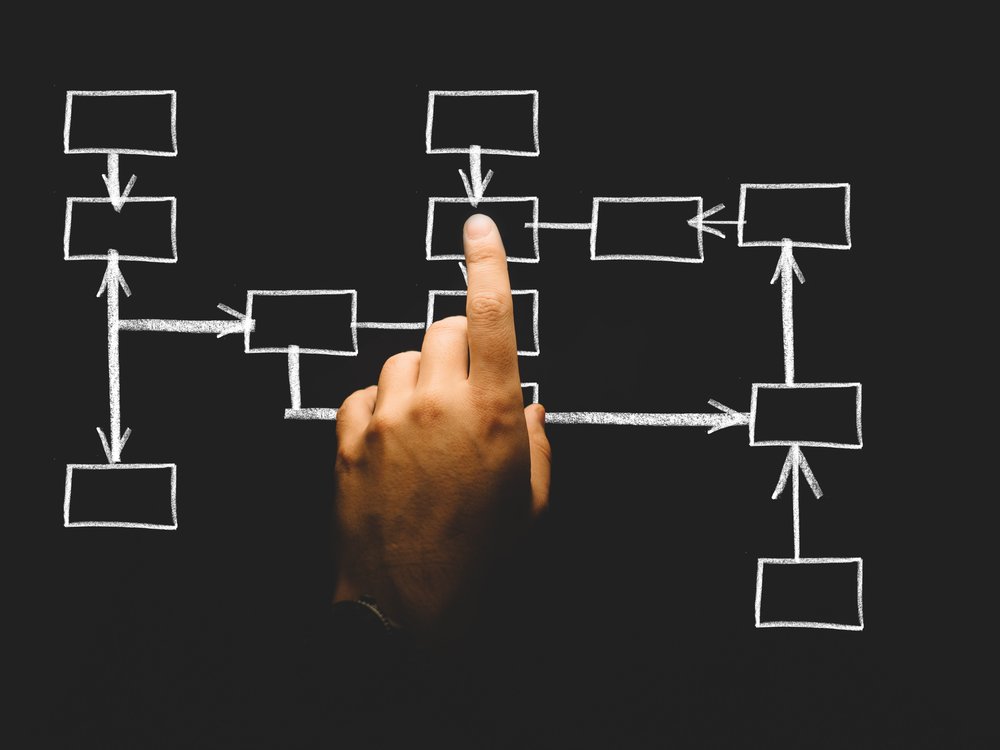
Our Methodology
We recommend a comprehensive, team-based approach gathering input for the major stakeholders across the cross-functional process.
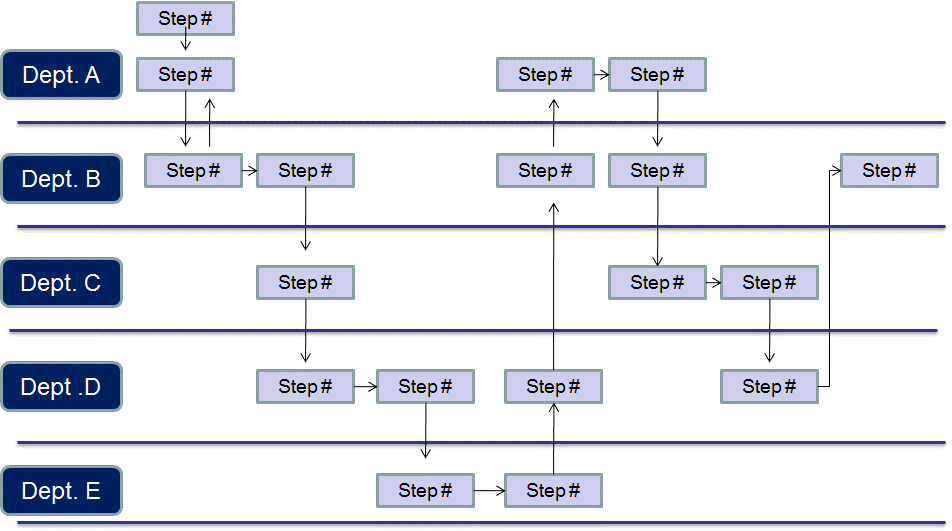
“As Is” Process
A narrow business process flow that can often decrease efficiency resulting in too many steps and poor-quality product. This is an example of an “As Is” Process Flow. Note the complexity, how many departments are involved, the number of steps, etc.
The message: simplify and execute a shorter, more efficient process to maximize your resources.
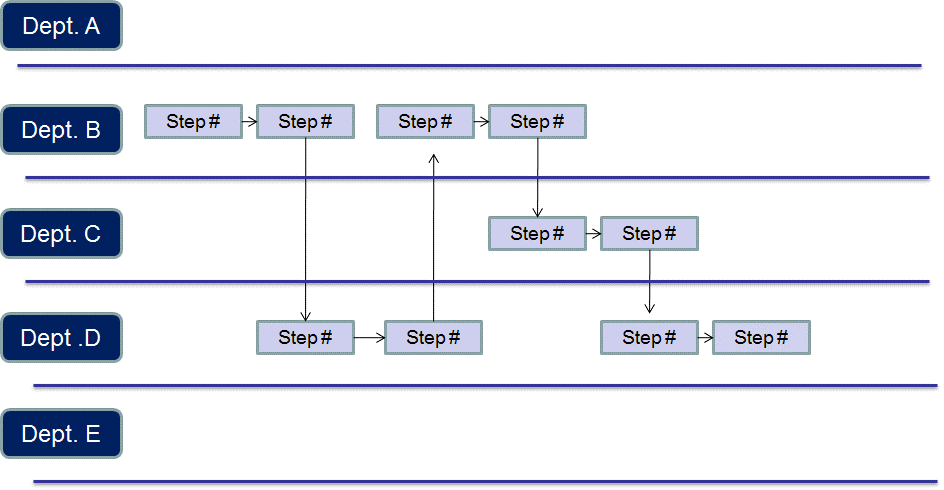
“To Be” Process
Here’s a list of “Trigger Verbs” – action-oriented verbs that will help ask the right questions to identify improvement opportunities. By applying these opportunities, the new “To Be” process will be developed.
Eliminate, Substitute, Standardize. Change Frequency, Simplify, Change Sequence, Reduce, Change Timing, Combine, Bring Inside, Automate, Outsource, Accelerate, Centralize, Defer, Decentralize, Do in Parallel, Reduce the Quality, Apply Lean, Apply Six Sigma, Apply Process Redesign, Value/Non-Value Activity Analysis. Cost of Poor Quality. Best Practices.
By applying Process Improvement and Lean/Six Sigma concepts to the “As Is” process, significant improvements in quality, cost, and speed can be achieved.
Timeline
Here’s a typical timeline to complete a process improvement project for a single process:
This can change based on the process scope, complexity, and level of detailed required.
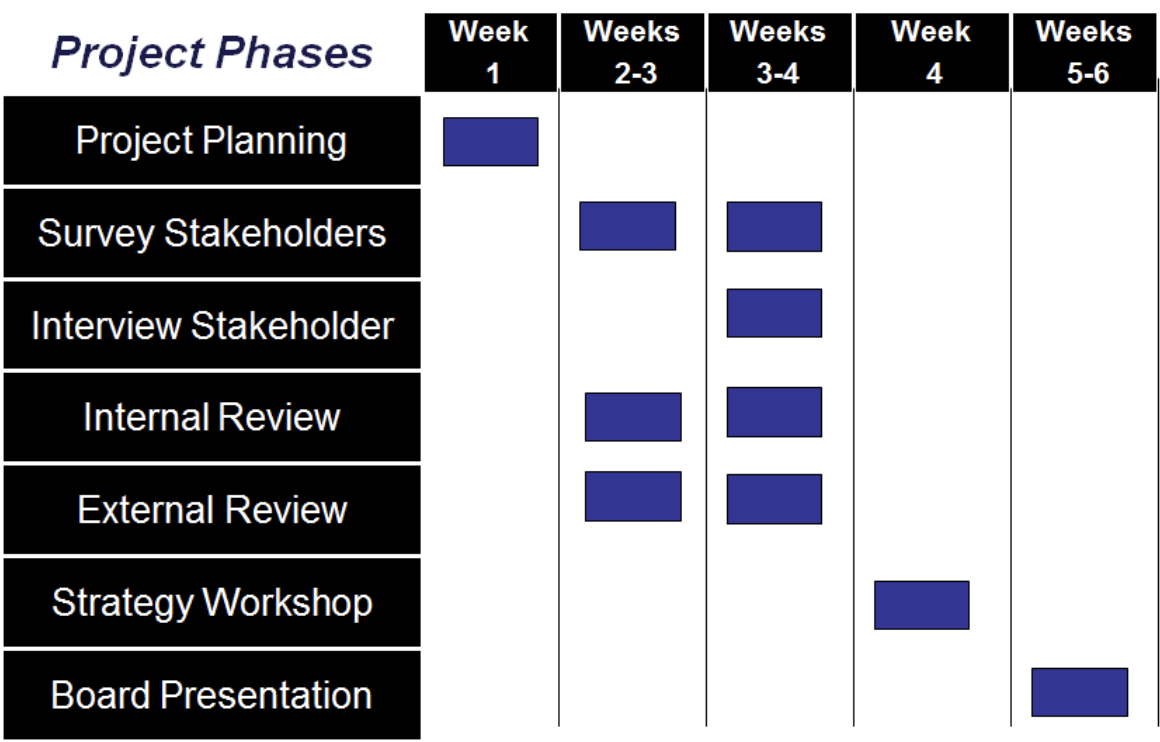
For more information, contact:
Steve Finkelstein at (314) 409-6869 and steve.finkelstein@experience-on-demand.com or
Ray Scott at (314) 304-8070 and ray.scott@experience-on-demand.com